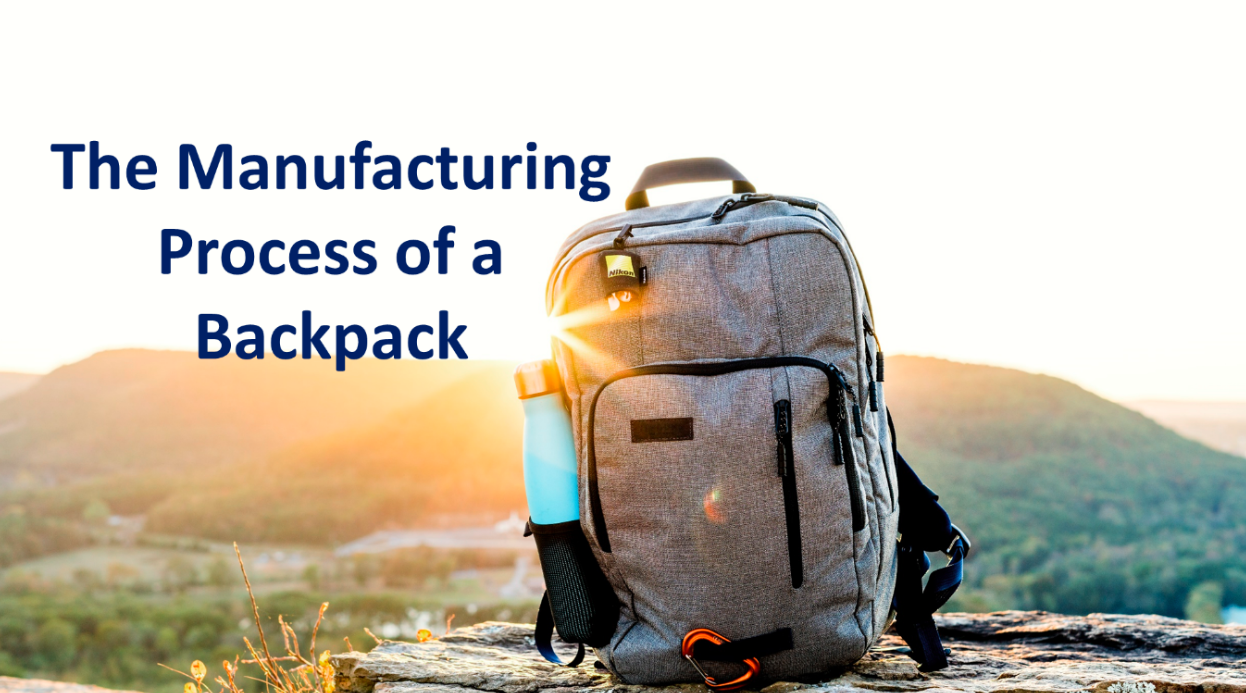
In the dynamic realm of sustainable fashion, Recycled Polyethylene Terephthalate (RPET) stands as a beacon of eco-conscious innovation. Among its diverse applications, RPET takes center stage in the creation of backpacks, transforming discarded plastic bottles into stylish, environmentally friendly accessories. This journey unveils the intricate process of crafting RPET backpacks, showcasing the transformation from waste to wearable, thread by thread.
Understanding RPET:
Recycled Polyethylene Terephthalate (RPET) is a recycled form of PET, a common plastic found in beverage bottles, food packaging, and various consumer products. The RPET manufacturing process involves collecting post-consumer PET items, processing them, and converting them into a recycled material suitable for textile applications, including backpacks.
1. Collection of PET Bottles:
The journey of RPET backpacks begins with the collection of discarded PET bottles. These bottles are sourced from recycling centers, waste management facilities, and collection initiatives. The collected bottles undergo a meticulous cleaning process to remove labels, caps, and any contaminants.
2. Shredding and Sorting:
Cleaned PET bottles are mechanically shredded into small pieces, creating raw material for the RPET production. The shredded material undergoes further sorting to eliminate any remaining impurities. This rigorous sorting process is critical to ensuring the purity and quality of the recycled material.
3. Melting and Extrusion:
The sorted PET flakes are subjected to a melting process, turning them into a molten form. This melted material is then extruded through small openings, creating thin strands known as filament yarn. These yarns become the building blocks for the fabric used in RPET backpacks.
4. Spinning into Yarn:
The extruded strands are spun into yarn through a spinning mechanism. This process aligns the polyester fibers, enhancing the strength and durability of the resulting yarn. The quality of the yarn is pivotal in determining the overall robustness and performance of the final RPET backpack.
5. Weaving or Knitting:
The RPET yarn is woven or knitted to form a textile structure. Weaving involves interlacing the yarn in a crisscross pattern, resulting in a tightly woven fabric. On the other hand, knitting involves creating interlocking loops of yarn, producing a more flexible and stretchable material. The choice between weaving and knitting depends on the desired characteristics of the final backpack.
6. Dyeing and Finishing:
The RPET fabric undergoes a dyeing process to add color. Emphasizing sustainability, eco-friendly dyeing methods are often employed. Following dyeing, the fabric may undergo finishing processes such as waterproofing or the application of special coatings to enhance its functional properties.
7. Pattern Cutting:
Dyed and finished RPET fabric is carefully laid out in layers, and pattern pieces for the backpack are precisely cut. Precision in pattern cutting minimizes waste and optimizes the use of RPET material, aligning with the sustainable ethos of the manufacturing process.
8. Sewing and Assembly:
The cut pieces are assembled through sewing, either by skilled artisans or automated machinery. This assembly process involves stitching together various components of the backpack, including the main body, pockets, zippers, and straps. The adherence to a predetermined design ensures consistency and quality in the final product.
9. Quality Control:
Stringent quality control measures are implemented at multiple stages of the manufacturing process. Inspection of the RPET material for imperfections, verification of pattern cutting accuracy, and examination of the stitching and assembly for defects are crucial steps. Rigorous quality control ensures that each RPET backpack meets the desired standards of durability and aesthetic appeal.
10. Branding and Final Touches:
Once assembled, the RPET backpacks undergo branding, adding elements such as logos, labels, and tags. Any additional features, such as adjustable straps, buckles, or specialized compartments, are incorporated during this stage. These final touches contribute to the distinctive identity of each RPET backpack.
11. Packaging and Distribution:
The finished RPET backpacks are thoughtfully packaged for transportation. Sustainable packaging options are often chosen to align with the eco-friendly nature of the product. The backpacks are then distributed to retailers or directly to consumers, ready to embark on their journey as stylish and sustainable accessories.
RPET Backpack Supplier:
The term “RPET backpack supplier” refers to a company or entity involved in the production and distribution of backpacks made from Recycled Polyethylene Terephthalate. These suppliers play a vital role in the sustainable fashion ecosystem by offering environmentally friendly alternatives to traditional backpack materials.
Choosing the Right RPET Backpack Supplier:
- Sustainability Credentials:
Seek an RPET backpack supplier with strong sustainability credentials. Consider their commitment to using recycled materials, eco-friendly production processes, and adherence to ethical labor practices.
- Product Quality:
Assess the quality of the RPET backpacks offered by the supplier. Consider the durability of the material, precision of craftsmanship, and overall functionality of the backpack. Customer reviews and testimonials provide valuable insights into the product’s quality.
- Customization Options:
Some RPET backpack suppliers offer customization options, allowing brands or businesses to create unique designs or incorporate specific features. If customization is a priority, choose a supplier that can accommodate such requests.
- Certifications and Standards:
Check if the RPET backpack supplier adheres to relevant certifications and standards. Certifications like the Global Recycled Standard (GRS) or OEKO-TEX® Standard 100 indicate a commitment to environmental and social responsibility.
- Transparency in the Supply Chain:
Choose an RPET backpack supplier that provides information about their sourcing, manufacturing processes, and supply chain partners. Transparency in the supply chain builds trust between the supplier and the end consumer.
Conclusion:
The manufacturing process of RPET backpacks embodies a journey of transformation, turning discarded PET bottles into fashionable, sustainable accessories. The role of an RPET backpack supplier is instrumental in offering environmentally conscious alternatives to the fashion market. By selecting the right supplier, consumers contribute not only to the reduction of plastic waste but also to the broader goal of fostering a circular economy. Each RPET backpack, crafted thread by thread, represents a tangible step towards a more sustainable and eco-friendly future.